Employing the MujinController platform to master depalletizing and overcome complex mixed-SKU challenges
When a major retailer engaged Mujin to automate a mission-critical distribution center (DC), they encountered a significant challenge: automating mixed-SKU depalletizing. Known for its complexity due to the unpredictable nature of workpieces, this task had long been deemed too challenging for automation. The retailer’s DC, which managed a vast array of products varying in shape, size, and weight, struggled with manual depalletizing operations that were not only slow but also prone to errors and physically taxing on the workforce.
Mujin’s objective was to overturn this long-held belief by developing a scalable automation solution that could handle the complexity of mixed-SKU depalletizing while achieving industry-leading picking rates and reducing error rates. Leveraging advanced vision systems, tactile feedback, and the MujinController platform, we set out to transform their operations by enhancing accuracy, throughput, and overall operational efficiency.
Identifying the Challenge
The distribution center was responsible for managing a diverse inventory of products. Manual handling slowed down operations and introduced errors while placing significant physical demands on the workforce. The need for a robust, automated solution was clear. However, the complexity of mixed-SKU depalletizing presented a challenge that had eluded automation providers for years.
Crafting the Solution
Our approach began with a detailed design phase, where our engineers collaborated closely with the retailer’s team to ensure seamless integration with their existing workflows. This phase was crucial for addressing the complexity of mixed-SKU depalletizing and ensuring that the automation solution could handle the diverse range of products managed by the distribution center.
The solution centered around cutting-edge mixed-SKU depalletizing robot cells, each equipped with the following:
Overcoming Obstacles
The implementation of robotic automation for mixed-SKU depalletizing was not without its challenges. The variability in pallet loads—often containing items with irregular shapes, difficult-to-grip surfaces, and a wide range of sizes—posed a significant hurdle. These complexities have traditionally made mixed-SKU depalletizing difficult to automate, requiring a solution that could maintain both speed and accuracy despite these variables.
To address this, Mujin integrated advanced robotic grippers capable of handling a broad spectrum of products. These grippers, powered by the MujinController platform, provided precise control and real-time feedback, allowing the system to adapt dynamically to the unique characteristics of each item. The ability to generate dynamic workpiece physics models in real time was crucial in achieving high levels of picking accuracy, even with challenging materials.
The MujinController platform’s real-time digital twin was pivotal in navigating these complexities. By creating a live, virtual representation of the physical environment, the platform enabled continuous monitoring and adjustment of the robot’s actions. This dynamic model ensured that the system could respond effectively to irregular and complex pallet loads, maintaining optimal performance and accuracy. Additionally, the digital twin provided a comprehensive data environment that facilitated ongoing refinement and optimization of the system.
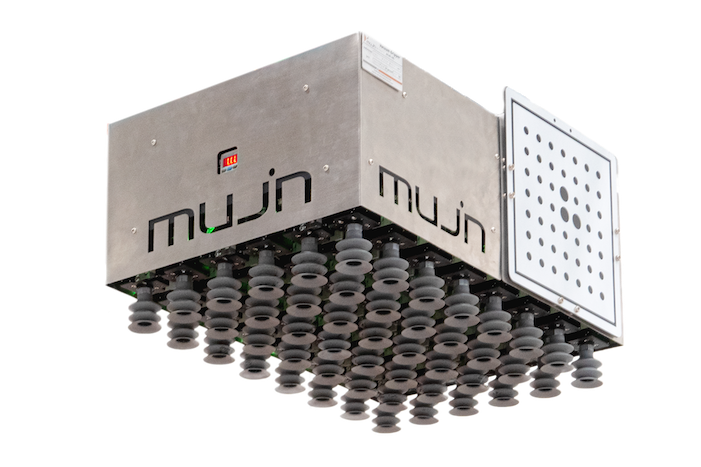
Another challenge was the need to upgrade the distribution center’s operations without causing significant disruption. Given the critical role of this facility in the retailer’s supply chain, minimizing downtime was essential. Mujin’s team meticulously planned the installation process, coordinating work during off-peak hours to ensure that the distribution center could continue its operations with minimal interruption. This strategic approach allowed for the seamless integration of the new system, demonstrating Mujin’s commitment to both innovation and operational continuity.
By leveraging the capabilities of the MujinController platform and a strategic approach to system integration, Mujin successfully overcame these obstacles. The result was a robust automation solution that met the retailer’s needs and set a new standard for efficiency, accuracy, and reliability in mixed-SKU depalletizing.
Seamless Implementation
The successful deployment of Mujin’s automation solution required a meticulous approach to ensure that every phase of the project was executed flawlessly. From the initial concept to the final go-live, each step was carefully planned and coordinated to deliver a seamless integration with the retailer’s existing operations. The focus was not just on installing advanced technology but on ensuring that this technology enhanced the overall efficiency and reliability of the distribution center without disrupting its critical daily operations.
Mujin’s implementation process was comprehensive, encompassing all major project phases:
The implementation also involved several key technical steps:
Delivering Results
The implementation of Mujin’s advanced automation solution at the retailer’s distribution center yielded transformative results, setting new benchmarks for efficiency, accuracy, and overall operational performance. By integrating the MujinController platform and leveraging cutting-edge robotics, the distribution center not only met but exceeded its operational targets, delivering significant improvements across key metrics.
The implementation of Mujin’s advanced automation solution at the retailer’s distribution center yielded transformative results, setting new benchmarks for efficiency, accuracy, and overall operational performance. By integrating the MujinController platform and leveraging cutting-edge robotics, the distribution center not only met but exceeded its operational targets, delivering significant improvements across key metrics.
Conclusion
Mujin’s automated depalletizing solution, powered by the MujinController platform, revolutionized operations at the retailer’s distribution center. The integration of the real-time digital twin was particularly impactful, providing continuous optimization and ensuring top-tier performance and accuracy. This project is a testament to Mujin’s ability to deliver cutting-edge solutions tailored to complex logistics environments, transforming challenges into opportunities for our clients.
As we continue to push the boundaries of what’s possible in automation, we remain committed to enhancing efficiency, accuracy, and productivity in distribution centers around the world.